The Art of Stopping: Unraveling the Mastery Behind Force Control’s Brake Systems
Brake systems utilizing oil shear technology offer significant advantages in industrial applications. Oil shear brakes […]
Beyond the Basics: A Closer Look at Force Control’s Innovative Clutch Technologies
Click to Expand Clutch technology is vital in seamlessly bridging power sources to mechanical systems. […]
The Evolution of Brake Motors: A Deep Dive With Force Control Industries
Brake motors combine a motor and braking system into one unit, offering advantages over traditional […]
Safety First: Unveiling the Power of Explosion-Proof Brake Motors at Force Control
Industrial safety is essential, particularly in high-risk sectors such as nuclear, aircraft, chemical, oil and […]
Master Guide to Heavy Duty, High Cycle Brake and Clutch Applications
Brake and clutch systems play a significant role in assuring the safety and efficiency of heavy duty manufacturing processes requiring high cycle rates. They are relied upon in various applications, including heavy machinery, mining equipment, and other industrial purposes.
Key Considerations in Industrial Brake and Clutch Systems
The proper functioning of industrial machinery heavily relies on the critical role of brake and clutch systems. They are responsible for regulating the movement and speed of the machinery while ensuring the safety of workers and equipment.
How to Choose the Right Industrial Clutch Systems
A clutch is a mechanical device that engages and disengages the power transmission. It also allows the controlled and smooth transfer of rotational power from a driving component (motor) to a driven device (machine).
What to Look for in Industrial Clutch and Brake Systems
A clutch and a brake may seem interchangeable at first glance, but they perform two distinct functions. A clutch is a transmission and control device that transfers energy from the driver to the driven shaft.
How to Choose the Right Industrial Motor Brake System
Industrial motors are used in various applications, such as manufacturing, mining, forest products, materials handling, and oil and gas. Often paired with brakes to improve performance, they work together to accomplish the intended purpose.
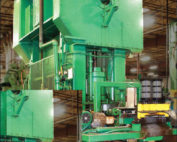
Oil Shear Clutch Cuts Downtime for Metal Stamping Press
Replacing a mechanical clutch, the oil sheer technology supplies constant, reliable tension on the stock feeding a 400-ton press to deliver precision and repeatability.
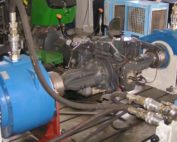
Dynamometers Suitable for High-Torque, Low-Speed
High torque, low-speed testing is often a challenge for dynamometers equipped with traditional load brakes.
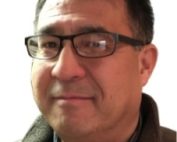
Force Control Announces New Western Regional Manager
Force Control Industries announces the addition of Mike Fox as new Western Regional Manager.
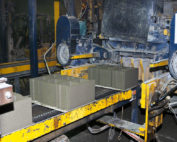
Oil Shear Cuts Machine Downtime
Ohio’s Reading Rock had limited idle time throughout a four-year stretch when the market was at or near peak.
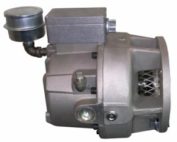
MagnaShear Hazardous Duty Brakes
New MagnaShear hazardous duty brakes from Force Control Industries, which employ oil shear technology to provide longer service life with virtually no maintenance or adjustment, now meet Class I and Class II Div 2 specifications (Div 1 in process with approval forthcoming).
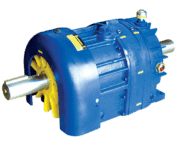
Clutch Brakes Providing Precise Positioning
Force Control Industries (Fairfield, OH) announced its fan cooled Posidyne clutch brakes which allow rapid and precise stopping, starting, speed change and positioning even in harsh environments.
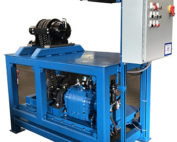
Dynamometers Featuring Positorq Load Brakes
Force Control dynamometers featuring Positorq Oil Shear load brakes absorb extreme torque at very low speed.
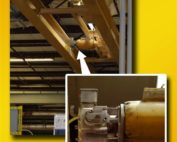
Force Control’s Latest MagnaShear Motor Brake for Cranes
Force Control Industries is producing a maintenance-free, no-adjustment crane brake that was designed to eliminate crane downtime.
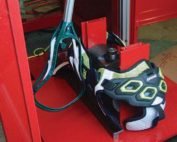
Oil Shear Clutch Brake Lets Lacrosse Stick Swing Realistically
Lacrosse stick OEM scores big using an oil shear clutch to test the durability of their product in game-like settings.
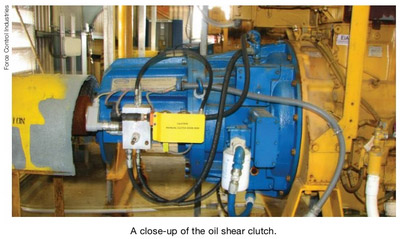
Staying Dry by ‘Going Wet’
Normal dry clutches employ a sacrificial surface — a disc or pad — to engage the load. With no good way to remove the heat caused from engagement between the disk and plate, this material must absorb the heat.
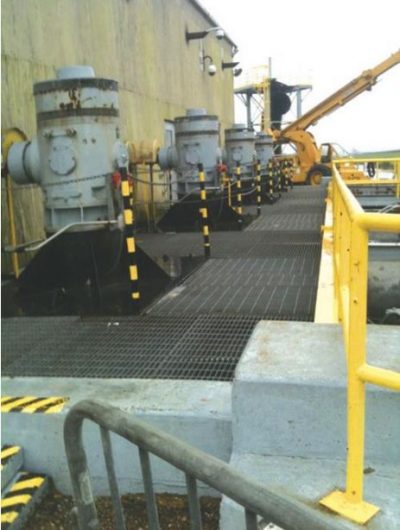
How a Wet Clutch Helps a NASA Facility Stay Dry in the Big Easy
Oil shear technology enables remote actuation of storm water drainage pumps and reduces downtime associated with maintenance.
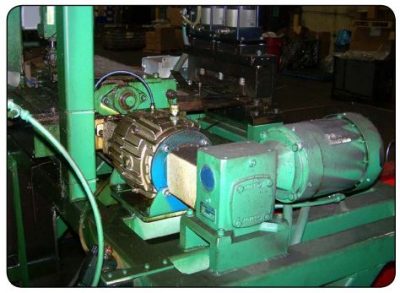
ART Technologies STAMPS OUT DOWNTIME WITH FORCE CONTROL’S OIL SHEAR TECHNOLOGY
ART Technologies relies on an oil shear clutch brake to supply constant, reliable tension on the coil feeding one of their 400-ton presses to give them the precision and repeatability they need, with no downtime for maintenance or adjustment.
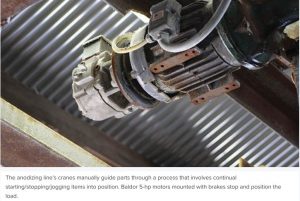
Oil Shear Brakes Cure Headaches
Running three shifts around the clock throughout the week doesn’t allow production downtime on the anodizing line at the Southern Aluminum Finishing Co. (SAF) site in Atlanta.
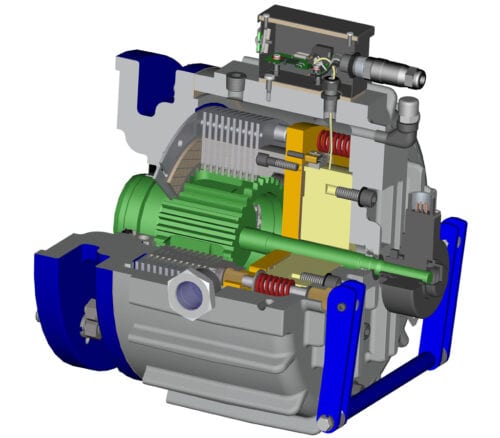
TECHNICAL REPORT – OIL SHEAR TECHNOLOGY PREVENTS DOWNTIME
A call from the second shift with maintenance troubles shouldn’t be among the things that keep you awake at night says US company Force Control Industries.
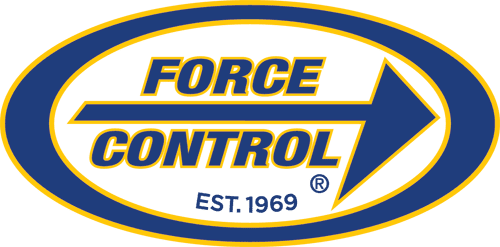
Automated Bakery Bets Its Dough on Oil-Shear Clutch/Brakes
30x Longer Life Reduces Maintenance Costs, Turns Clutch/Brake Replacement Time Into Productive Uptime